La empresa de soluciones de clasificación magnética y por sensores Steinert ha creado una nueva planta de pruebas en la mina de oro de Navachab, cerca de Karibib, en Namibia, propiedad de la empresa de capital privado QKR. La instalación está disponible para realizar pruebas en los procesos de beneficio y preconcentración.
¿Cómo es posible que un cliente de Steinert abra la puerta para apoyar a otros clientes potenciales de Steinert en África y dé luz verde a una instalación de pruebas en su planta? Hildebrand Wilhelm, director de procesamiento de mineral de las operaciones de QKR Namibia Navachab, con 34 años de experiencia en la industria minera, afirma que la capacidad y los resultados satisfactorios, así como las buenas relaciones con Steinert, le llevaron a hacerlo.
Cuando los márgenes de costos se estaban comiendo los beneficios de la mina, Wilhelm y su equipo de la mina de oro de Navachab empezaron a emplear una nueva tecnología en la minería: la clasificación del mineral mediante sensores debía mejorar la ley del oro y eliminar el material inútil que no supondría una carga para los procesos siguientes y debería suponer un ahorro de costos. Eso fue hace seis años.
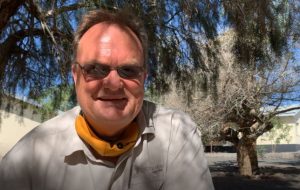
Desde 2016, dos sistemas de clasificación a granel por transmisión de rayos X STEINERT XSS-T están instalados en una planta de producción de 200 t/h para mejorar el material de las pilas de baja ley.
“Lo que nos ha sorprendido es, que la máquina es muy robusta. Estamos obteniendo una buena fiabilidad en las unidades y el 80-90% de tiempo de funcionamiento es absolutamente posible”, comenta Wilhelm. “Creo que es un reto buscar nuevas tecnologías en un entorno minero muy conservador. Es muy importante tener confianza en la gente con la que se trabaja”, prosigue.
La mina de oro de Navachab se arriesgó y aprendió que con las capacidades de Steinert era posible innovar en la industria minera, y pudo reducir los costos de procesamiento.
“Hemos configurado las plantas de tal manera que obtenemos un 25% de extracción en masa para concentrarnos y conseguimos una media del 70% de recuperación de oro con este tipo de configuración: eso tiene sentido para nosotros. Es una operación rentable. Tratamos el material en las máquinas XRT y, en general, duplicamos la ley de nuestro material de entrada y ahí es donde se genera el valor porque entonces, con la ley duplicada, el material puede ser tratado de forma rentable por los procesos que vienen después”, complementa el ejecutivo de Steinert.
Prueba en África
Wilhelm lo dice por experiencia: “El equipo de Steinert en Namibia es un equipo que conozco desde hace mucho tiempo. Soy muy consciente de sus capacidades y han estado dispuestos a ayudar”. Situado en Namibia y en el lugar, John Knouwds, director de ventas de la zona de Steinert para el sur de África, está encantado de ayudar a los mineros que quieran probar lo que la clasificación puede hacer por sus procesos en la planta de pruebas in situ.
“La preconcentración ahorra mucha energía, agua y, por tanto, dinero, porque un equipo posterior solo procesa el material con minerales valiosos”, indica John Knouwds. La instalación en la planta de Navachab permitirá a Steinert seguir realizando pruebas para diversas minas y proyectos de procesamiento en todo el sur de África. La propia planta de Navachab podrá realizar pruebas de viabilidad, que es una forma de analizar la capacidad de los sensores para clasificar el material mineralizado y no mineralizado, así como la eficacia de una separación teórica.
La planta de pruebas proporcionará datos tangibles de expectativas de producción mejoradas y sostenibles para los inversores, y mejorará las perspectivas económicas para determinar mejor las oportunidades asociadas a las inversiones.
Nueva planta de ensayos in situ
Se trata de una unidad combinada, capaz de manejar un rendimiento de entre 5 t/h y 100 t/h con un ancho de trabajo de 1 m. La unidad incluye un sensor de transmisión de rayos X (XT) para identificar las densidades atómicas, dos sensores ópticos -un sensor de color (C) y un sensor láser para información de forma 3D (L)- y un sensor de inducción (I) que detecta metales.
La unidad se desarrolló como respuesta a los requisitos cada vez más complejos de la separación de materiales. “La tecnología de Steinert ha dado un salto adelante al ofrecer múltiples sensores en una sola plataforma. Esto permite una mayor capacidad de clasificación, mayor capacidad de procesamiento, mayores recuperaciones y mejores grados”, explica Knouwds.
Disponer de la combinación correcta de sensores abre nuevas posibilidades para limpiar los productos generados más allá de lo que se requería originalmente o para añadir etapas de clasificación que antes se consideraban inviables. El software de Steinert, especialmente desarrollado, también permite diseñar nuevos algoritmos de detección, que pueden implementarse según sea necesario para hacer frente a nuevos retos.