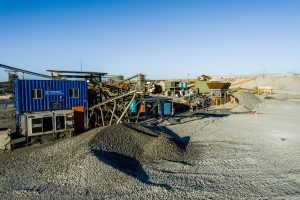
La demanda mundial de litio está aumentando debido a la generalización del uso de vehículos eléctricos y las baterías de iones de litio a escala de red para almacenar energía. Algunas previsiones auguran que la demanda alcanzará 1.5 millones de toneladas métricas de carbonato de litio equivalentes para 2025 (el triple que en 2021) y más de 3 millones de toneladas para 2030.
Este gran aumento de la demanda hace que resulte muy complicado satisfacerla. Aunque existen proyectos para aumentar la capacidad de extracción de litio en 2023 y 2024, el aumento de las ventas de vehículos eléctricos seguirá ejerciendo presión sobre el suministro.
Estas tendencias se traducen en un enorme potencial empresarial para las empresas extractivas. Sin embargo, mientras los nuevos proyectos pugnan por satisfacer la demanda, este potencial viene acompañado del reto de extraer de las minas tanto mineral de litio y de forma tan eficiente como sea posible, siempre en cumplimiento de unos requisitos medioambientales cada vez más estrictos.
Contaminación por basalto: el reto en la extracción de litio
El principal reto en la extracción de litio es la contaminación por basalto. Este material infértil con elevado contenido de hierro tiene una densidad alta muy similar a la de la espodumena. Esto implica que al utilizar la separación de medios densos (DMS) como forma principal de concentración de espodumena, el basalto se concentra con la espodumena y contamina el producto final.
Este problema se puede abordar extrayendo de forma selectiva mineral de elevada calidad, pero la contaminación es inevitable. Este método DMS genera así un producto defectuoso no apto para vender a precio de mercado. Este producto contaminado suele almacenarse, dejando sin explotar valiosos recursos de litio. Además, la DMS y los circuitos de trituración utilizados para producir concentrado de litio a partir de mineral consumen mucha energía y el tener que procesar producto contaminado en la planta reduce la productividad e incrementa los costos del proceso.
Las empresas extractivas deben maximizar la eficiencia de sus plantas de procesado utilizando su capacidad de forma eficaz para extraer de las minas tanto litio valioso como sea posible.
Una respuesta a este reto la tiene Tomra Mining, que cuenta con tecnologías probadas que pueden eliminar de forma eficaz la contaminación por basalto antes de la trituración. De este modo, se optimiza la capacidad de la planta de procesado, se reduce el consumo de energía y el tratamiento de los residuos lo que reduce el impacto ambiental del proceso.
Asimismo, estas soluciones permiten a las empresas extractivas alcanzar la calidad de producto necesaria y ampliar su proceso para incluir más material mineral contaminado con hierro y basalto.
Lee también ► Neumáticos para cargadores frontales que mejoran la movilidad y productividad
Valorizar el material desaprovechado con una clasificación basada en sensores
Las soluciones de clasificación basada en sensores emplean cámaras de color, sensores de transmisión de rayos X y láseres de escaneado multicanal para clasificar el mineral antes del tratamiento húmedo posterior. Los sensores analizan cada partícula, identifican el mineral y los residuos en milisegundos y chorros de aire de alta velocidad dirigen las partículas hacia las tolvas de producto o de residuos.
Estos equipos tienen una alta capacidad y procesan hasta 350 toneladas por hora en una única clasificadora. Con sus sensores clasifican, con una alta velocidad, un amplio rango de tamaños, de entre 6 mm y 200 mm. Optimizan la eliminación del hierro y el basalto del material, y reducen al mínimo los finos sin clasificar que se descartan o se almacenan. Además, han demostrado su eficacia en la reducción sistemática de la contaminación del mineral a menos del 4 %.
Esta fue la experiencia de Galaxy Resources en su mina Mt. Cattlin de Australia Occidental, donde una clasificadora Tomra PRO Secondary Laser lleva funcionando desde 2021 para reducir la contaminación de basalto en la pegmatita. Desde el primer día de funcionamiento, ha cumplido y superado todas las expectativas, logrando sistemáticamente menos de un 4 % de basalto en el concentrado.
Las eficiencias operativas se pueden mejorar mediante la conectividad que ofrece Tomra Insight, un servicio de suscripción basado en la nube que convierte las clasificadoras en dispositivos conectados capaces de generar valiosos datos del proceso. Con él, las empresas extractivas pueden medir el nivel de contaminación en tiempo real y, por tanto, la calidad del producto. Asimismo, pueden supervisar la distribución de los tamaños de partícula y, en consecuencia, la eficacia del equipo de trituración y cribado en los procesos posteriores. Tomra Insight también ofrece visibilidad sobre la capacidad y el uso de cada clasificadora, lo que permite optimizar el proceso casi en tiempo real. Además, permite al operario hacer un seguimiento preciso de los fallos que se producen en cada momento y mejorar los procesos de mantenimiento, para que la planta de clasificación funcione siempre al máximo nivel.
Una solución hecha a medida
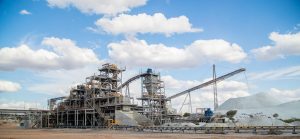
Tomra colabora estrechamente con sus clientes, ayudando a los clientes desde la fase de desarrollo hasta la compra y la integración en la planta, sometiendo las muestras de la mina a ensayos de calidad en su centro de pruebas y ofreciendo orientación al respecto. Su solución integra a el proceso de clasificación dentro del flujo global del proceso para lograr un funcionamiento fluido de la operación. Las clasificadoras se programan para adaptarse a la capacidad de la planta de triturado y cribado, así como a la planta de tratamiento húmedo, maximizando de este modo la productividad.
Este fue el enfoque para diseñar la planta de clasificación de litio más grande del mundo para Pilbara Minerals, en Australia. Tomra trabajó codo con codo con el equipo metalúrgico del cliente, completando un programa intensivo de ensayos en su centro de pruebas en Sídney. Allí se procesó una muestra del material de la mina australiana con clasificadoras que funcionaban en las mismas condiciones que en una planta real. Los buenos resultados obtenidos durante las pruebas y su experiencia y habilidad para proporcionar asistencia local experta hicieron que la compañía consiguiese la adjudicación del contrato.
Cabe destacar que la compañía también contribuyó en el diseño de la planta para definir el impacto que tendría el proceso de clasificación en la parte anterior y posterior del proceso de clasificación, y fue responsable de la puesta en marcha operativa y la optimización técnica.
Con las soluciones de clasificación de minerales basada en sensores, las empresas extractivas no solo mejoran la eficiencia de sus plantas de procesado, sino que además valorizan los materiales de desecho almacenados. También pueden ampliar sus recursos, explotando materiales minerales con mayor contaminación o buscar nuevas oportunidades de extracción en zonas con mayor contenido de hierro o basalto.