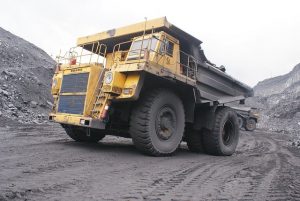
En Perú, alrededor del 80% de los motores que utiliza la industria son de eficiencia baja o estándar, y cerca del 95% ubicados en la minería no se le aplica la digitalización; además, estos equipos representan altos gastos de mantenimiento y más del 70% del consumo eléctrico en el sector industrial, según indica el Ing. Abraham Villanueva, especialista en eficiencia energética del negocio Motion de ABB en Perú.
Los motores estándar o de baja eficiencia energética generan un alto consumo eléctrico en el sector minero. Se calcula que en promedio una minera peruana pagaría más de USD 1.5 millón mensuales por la energía desperdiciada por estos equipos.
Así lo estima el especialista en eficiencia energética del negocio Motion de ABB en Perú, quien asegura que las pérdidas económicas al elegir un motor pueden ascender hasta 100 veces el precio de adquisición del mismo. Tanto por el desperdicio de energía a lo largo de su vida útil debido a su baja eficiencia, como también por la menor robustez, que puede causar paradas inesperadas en la producción. Es decir, si el equipo costó USD 1.000, las pérdidas promedio por parada serían hasta de USD 100.000 por día.
El Ing. Villanueva indica que el motor eléctrico de baja eficiencia energética no solo genera altos consumos de energía, sino que puede sufrir desperfectos mecánicos y causar inconvenientes en la producción (vibraciones recurrentes, altos picos de voltaje y daños en aislamientos) al punto de suspender la producción por horas, incluso semanas.
Lee también ► Anglo American completa su flota de tres palas eléctricas en proyecto Quellaveco
Alta eficiencia energética
Ante estos problemas, ABB desarrolló los motores eléctricos MMAS que son de eficiencia premium y que, en reemplazo de sus pares de baja eficiencia, reducen la facturación de energía eléctrica, así como los costos de mantenimiento y de paradas inesperadas en 5%, acumulando mayores ahorros durante la vida útil promedio de 20 años del nuevo motor. Además, si se complementa con variadores de velocidad en aplicaciones de torque variable pueden disminuir su consumo hasta en 50%.
De esta manera, con los motores MMAS de ABB en toda su base instalada, la industria podrá reducir sus costos de consumo eléctrico, mantenimiento y parada de planta de forma sustancial, según el tamaño de su parque instalado de motores, ya que se obtendrían ahorros de alrededor de USD 200.000 a lo largo de su vida útil por migrar un solo motor de 200HP baja eficiencia a MMAS.
Sobre los imperfectos que puede tener un motor, ABB ha sumado a los nuevos motores mejores componentes para ganar mayor robustez y operar en ambientes severos desde nivel del mar hasta los 5,000 m.s.n.m., donde es frecuente la alta presencia de polvo, humedad, vibración y temperaturas extremas, tales como chancadoras, molinos, celdas de flotación, fajas transportadoras, máquinas de bombeo, los cuales deben permanecer activos 24/7 sin alterar la productividad de las industrias.
Digitalización
Incluso, se pueden lograr ahorros incrementales con la digitalización de los motores, considerando que el 95% de ellos en la minería de nuestro país no cuenta con sensores de medición inteligentes, según comenta el especialista en eficiencia energética de ABB Perú. Actualmente, el monitoreo de muchos motores aún se realiza de manera presencial con personal de la empresa que debe recorrer hasta kilómetros para acercarse a los motores de una máquina de bombeo o una faja transportadora pudiéndose hacer de forma remota.
En el mercado peruano, ABB comercializa un sensor inteligente aplicado a los motores eléctricos, mediante el cual se pueden monitorear los niveles de vibración, temperatura, consumo de energía, entre otros parámetros del motor. “La data es enviada a la Nube y puede ser vista mediante una celular, tableta u ordenador, para su evaluación y toma de decisiones inteligentes”, argumenta Abraham Villanueva.
Finalmente, el representante de ABB asegura que con el sensor inteligente se evita la pérdida de tiempo y dinero “Se puede prever las fallas en el motor hasta por 1 mes para actividades de mantenimiento y 2 meses para paradas de planta, cuando resulten necesarios, logrando así ahorros significativos por paradas inesperadas”, puntualiza.